5 Ways Hot Melt Adhesives Can Help Overcome Labeling Challenges
Time:2017-11-03 From:
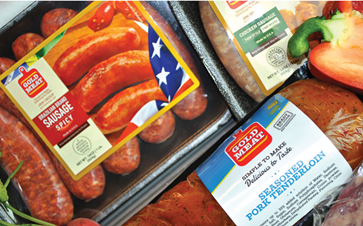
The labeling sector of the cold food and beverage packaging market can be a challenging business. From the extreme cold, wet, freezing or changing application conditions to difficult-to-adhere-to substrates, cold food and beverage manufacturers, and their co-packagers have their work cut out for them.
However, those who partner with label suppliers equipped with the latest advancements in hot melt adhesive technology are facing these challenges with a little more gusto. Hot melt adhesives are known for their unique manufacturing process – resulting in equally unique adhesive characteristics. And, for some cold food and beverage manufacturers, these unique characteristics are just what they’ve been looking for.
Of course, every application is different and a hot melt adhesive may not be the best option, but for applications that point to areas in which hot melts excel, these adhesives are proven game-changers. The following highlights several ways hot melt adhesives are helping some cold food and beverage manufacturers and co-packagers overcome labeling challenges.
1. Temperature Application Versatility
One of the greatest challenges of cold food and beverage labeling is the wide range of temperatures present. In frozen foods labeling, where temperatures are 0°F or below, adhesives can lose strength, stiffen and fall off. In refrigerated labeling, transporting products, such as meat and cheese, from store to home can cause label flagging if outdoor temperatures are hot and humid. Similarly, in beverage labeling, moving bottles from cold refrigerators to warm cars, for example, creates condensation that can affect label performance.
To meet the demands of such vast temperature ranges, some label suppliers have been able to specially formulate all-temperature hot melt adhesive labels. With these labels, neither sub-zero temperatures nor heat is an issue. Labels remain adhered to packages from temperatures as cold as -65°F (-54°C) to temperatures as warm as 150°F (65°C). Additionally, they can be applied at temperatures as low as -10°F (-23°C), which is especially beneficial for products that are packaged, shipped and stored in cold temperatures.
2. Better Flow
Another common challenge in cold food and beverage labeling is the wide variety and type of product packaging materials used. Most cold food and beverage packages are made of low-surface energy (LSE) substrates, such as low-density polyethylene (LDPE), high-density polyethylene (HDPE), cardboard, plastic films, polypropylene and polyester, which are difficult to adhere to when it comes to labeling.
For example, in cheese applications, shrink film is a commonly used packaging material. However, shrink film tends to harden in cold temperatures and when cheese is packed, transported and stored, temperatures usually range from 34°F to 38°F. Another common packaging example is corrugate. Corrugate is lightweight, low cost and has ideal graphics capabilities, as well as an established recycling infrastructure – it is also one of the most challenging substrates for label adhesion.
With hot melt adhesives, specifically all-temperature hot melts, cold food and beverage manufacturers and co-packagers can achieve conformability and adhesion to a wide variety of packaging types. Compared to some adhesives that become harder at colder temperatures, hot melt all-temperature adhesives flow better at colder temperatures, allowing the adhesive to flow better onto the package. Because of this unique adhesive chemistry, hot melt adhesives stick better to LSE substrates than other types of adhesives. And, given the high number of LSE materials used in cold food and beverage packaging, hot melt adhesives offer a superior labeling option for cold food and beverage manufacturers and co-packagers.
3. Non-Water Whitening Properties
For cold food and beverage manufacturers who use clear product labels, label integrity is another highly anticipated concern. When some adhesives get wet, clear labels can take on a milky white appearance – which can be detrimental to a product’s brand and shelf appeal.
Hot melts are formulated with superior water resistance and non-water whitening properties so they can stand up to dampness and maintain both adhesive integrity and aesthetic appeal. With hot melt adhesives, even if exposed to water or moisture, brand owners who use clear labels can trust labels will continue to perform as intended.
4. Secure, Lasting Adhesion
It’s no secret it can be difficult to find an adhesive that meets cold food and beverage durability requirements. In addition to temperature extremes and potential moisture, many cold food and beverage packages also go through repeated product handling. Meat and poultry products are a great example. The last thing a meat or poultry brand owner wants is for a label to degrade or come off their high-priced item’s package before the end-user is finished with it – or, worse yet, before making it to the end-user.
Hot melt adhesives are known for their excellent quick stick and initial bond properties. Due to the adhesive composition of hot melts, they are made to stick and stay in place for the lifetime of the product.
5. Environmentally and Economically Friendly
Throughout the cold food and beverage supply chain, manufacturers, co-packagers and others strive to be good stewards of the environment – and, their bottom lines. However, finding product labels that successfully accomplish both can be challenging.
For those looking to achieve superior environmental and economic goals, choosing a hot melt adhesive label is a great option. As opposed to other adhesive manufacturing methods, neither solvents nor water is used in the coating process. This eliminates the need for adhesive drying in long conventional gas-fired ovens, as is common with other adhesive manufacturing. Instead, hot melts dry quickly by way of a cooling drum – resulting in a manufacturing process that significantly reduces overall energy consumption.
Additionally, because no solvents are used, hot melt adhesives also allow for ultra-low levels of VOC out-gassing, migration and residuals – making them environmentally safe. Other benefits include increased production efficiencies, a smaller physical footprint, less preparation and resources (i.e., raw materials), and, generally, lower overall costs.
Without doubt, hot melt adhesive labels are helping some cold food and beverage manufacturers, and co-packagers overcome package-labeling challenges. If you are facing these or similar challenges in general refrigerated and frozen foods labeling, beverage labeling, meat and poultry labeling, cheese labeling or other cold food labeling, consider hot melt adhesive labels for your next application. They just may be the answer you’ve been seeking.
News Source:Flexible Packaging
Written By Kim Hensley&Kathy Magyar