Hamillroad Software – Screening technology for expanded colour gamut printing
Time:2018-07-03 From:
Written by Andy Cave
The most notable barriers to achieving the required success in offset and flexo printing are halftone screening and controlled ink transfer
The problems with halftone screening
The conventional AM halftone screening, as well as hybrids such as XM has several problems which reduce the success of using ECG printing:
- ·Screen angles / moiré / angle clashes
- ·Rosettes and colour shifts
- ·Large mid-tone dots
- ·Grainy or noisy flat colours
To eliminate visible screening moiré, the angles of the halftone screen for each colour must be 30° apart; this is only possible for three screens in a CMYK ink set. One of the colours, typically the Yellow, will always produce moiré. With yellow, moiré is not as visible to the naked eye because it is a very light colour.
The problem arises when there are more than four process colours used to build screen tints: as there are no more screen angles available to use, this can result in moiré ruining the integrity of the simulated spot colour.
A bi-product of screen angles is a rosette: a high-frequency moiré pattern. Rosettes have a frequency, an lpi, which is half the lpi of the screen, for instance; a 200 lpi AM/XM screen has rosettes with an lpi of 100. An lpi of 100 is low enough to be easily visible and results in a grainy (or noisy) patch, instead of rendering a smooth flat colour build. A further characteristic of conventional screening is that the halftone dots vary in size throughout the tone scale.
FM screening – a possible solution?
While FM screening does eliminate some of the problems associated with AM/XM, it comes with its own set of drawbacks: Implementing FM screening requires an almost laboratory standard of plate-making and printing environment to achieve satisfactory results on press.
FM can be challenging to use in offset, but it’s extremely difficult to implement in flexo. For many printers, the size of the dots and the patterns created in FM can contribute to an unacceptable grainy, noisy, appearance in flat screen tint builds.
Digitally Modulated Screening (DMS) (Auraia DMS for offset and Bellissima DMS for flexo) might appear to be just another form of FM screening. However as a FM screening technique, DMS eliminates screen angles and rosettes, and the dot sizes are uniformly distributed in size through the tone scale.
DMS is matched to the platemaking and press conditions, controlling the dots in each colour and between the colours. DMS achieves the high-level of image detail associated with FM stochastic screening while producing smooth, noise-free, flat tints.
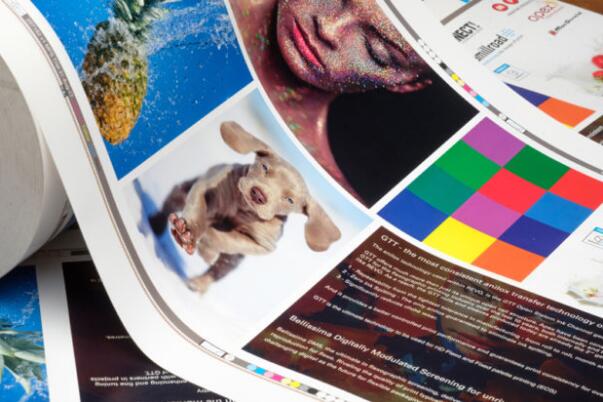
Controlled ink transfer
The colour simulation software packages available today are reliably consistent.
Increasingly, printers need to be able to “print by numbers,” using LAB and density as well as managing all the variables involved in the print process. The market needs a way to eradicate the variables, in turn, eliminating the complexity associated with managing them.
Apex GTT provides a consistency of ink transfer for flexo printers which creates a stable foundation for ECG printing and, when used in conjunction with Bellissima DMS, eliminates many of the problems related to ECG and gives the printer a “best in class” process solution.
What is Bellissima Digitally Modulated Screening (DMS)?
The Bellissima DMS screening technology for flexo includes features such as 100% solid surface patterning options and solid object protection.
This screening digitally modulates every pixel it produces thereby precisely controlling the dots in each separation while its “stochastic rosette” interleaves the screens in the separations to eliminate noise and moiré. The stochastic rosette maximises the ink-on-paper area and minimizes the amount of ink-on-ink, to expand the available colour gamut while eliminating colour shifts due to mis-registration.