3D Printed Cars – HP Introduces the Metal Jet
Time:2018-10-08 From:
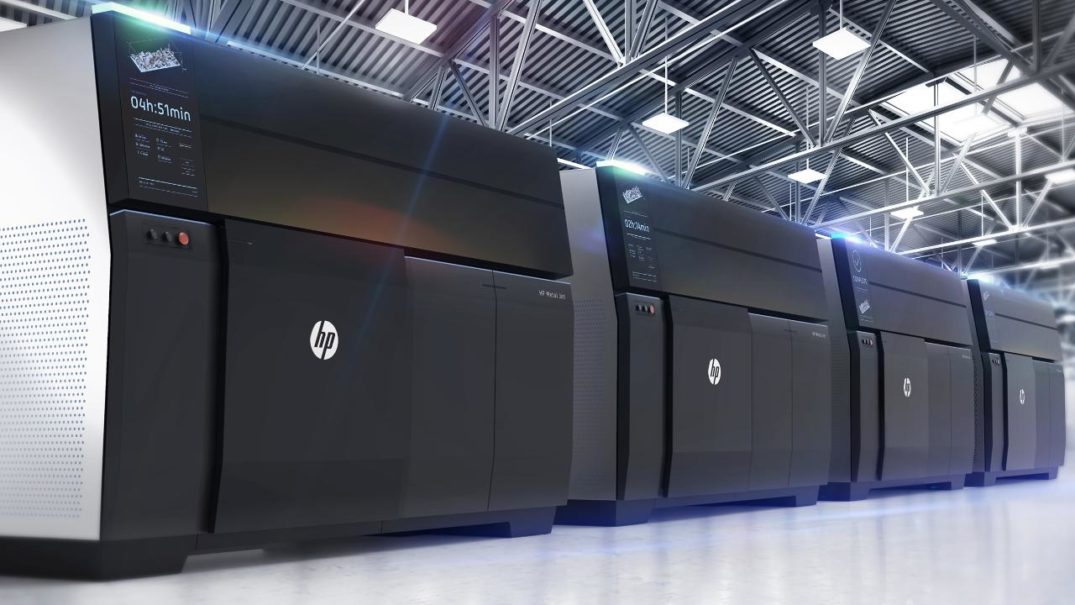
When it comes to 3D printing, many people think of small plastic products like those from MakerBot. The computer and printer manufacturer HP is already thinking a little bigger. They recently announced the Metal Jet, an industrial 3D printer that can process steel.
3D plastic printers are often used for custom products such as prostheses and hearing aids. They also make it easier for product designers to develop prototypes. But compared to industrial production as a whole, these applications occupy small niches. The reason for this is that 3D printing is still relatively slow and expensive. In addition, only a limited selection of materials can be processed.
HP has been trying to change that for some time. In 2016, the company launched its Jet Fusion 3D plastic printer, which is designed for mass production rather than one-time printing. With the Metal Jet, the company aims to enter the automotive production sector or the manufacture of medical devices.
The Pace of Innovation Will Increase
HP is partnering with Parmatech, a medical technology company, and GKN, a supplier to the automotive and aerospace industries. These partners, in turn, will work with customers like Volkswagen to experiment with the 3D metal printer. In exchange, they will already receive the necessary equipment this year. The rest of the market will have to wait until 2020.
Many of the products printed with the Metal Jet are still small accessories, such as key rings with individual engravings. It will still take some years before it is possible to buy a car that parts from the 3D printer under the engine hood. But Tim Weber, HP’s 3D metals manager, says that 3D printing will reduce manufacturing costs for certain components and allow companies to develop new products faster. In some cases, companies could use the same designs for prototyping and then production. “Many parts take months to prototype,” he says. “We can now do in days what we used to take months or years to do. The pace of innovation will increase as a result”.
Others have been using 3D metal printing for years. For example, GE Aviation produced a fuel nozzle for one of its engines using a process called laser sintering. Unfortunately, this process is slow and expensive. It may work for extremely expensive engine components, but it is not practical for the countless other metal parts that are produced daily around the world.
Binder Jetting: Printing with Metal Powder
HP uses another process called binder jetting, which Weber says is cheaper and more efficient. The Metal Jet printer, which looks like a bigger version of a photocopier, distributes metal powder layers and then sprays them with a binder to solidify them.
The objects, which essentially consist of metal dust that is stuck together, are not very stable at first. Thin pieces can be broken with bare hands. The parts are then placed in an oven where the extreme heat solidifies the powder. The end result is relatively light and smooth and can contain surprisingly fine details. Customers can choose from a variety of alloys, and HP is working with various suppliers to make their materials available for the Metal Jet.
HP is not the first company to use Binder Jetting for metals. The 3D printer manufacturer EXone has been using this technology for years. The start-up company Desktop Metal also launched competing products last year. However, Tim Weber believes that HP will gain the higher ground in the competition due to its experience in manufacturing conventional printers. The company’s 3D printers and 2D printers share many components, most notably the nozzles for spraying ink, plastic or metal. Because HP manufactures millions of nozzles, it can also produce them more cheaply. This also means that technicians trained to maintain and support conventional industrial printers need little additional training to repair the new metal printers.
Since the possibility of manufacturing metal products in small batches at low cost has not yet existed, we will have to wait and see how companies use the technology in the future.